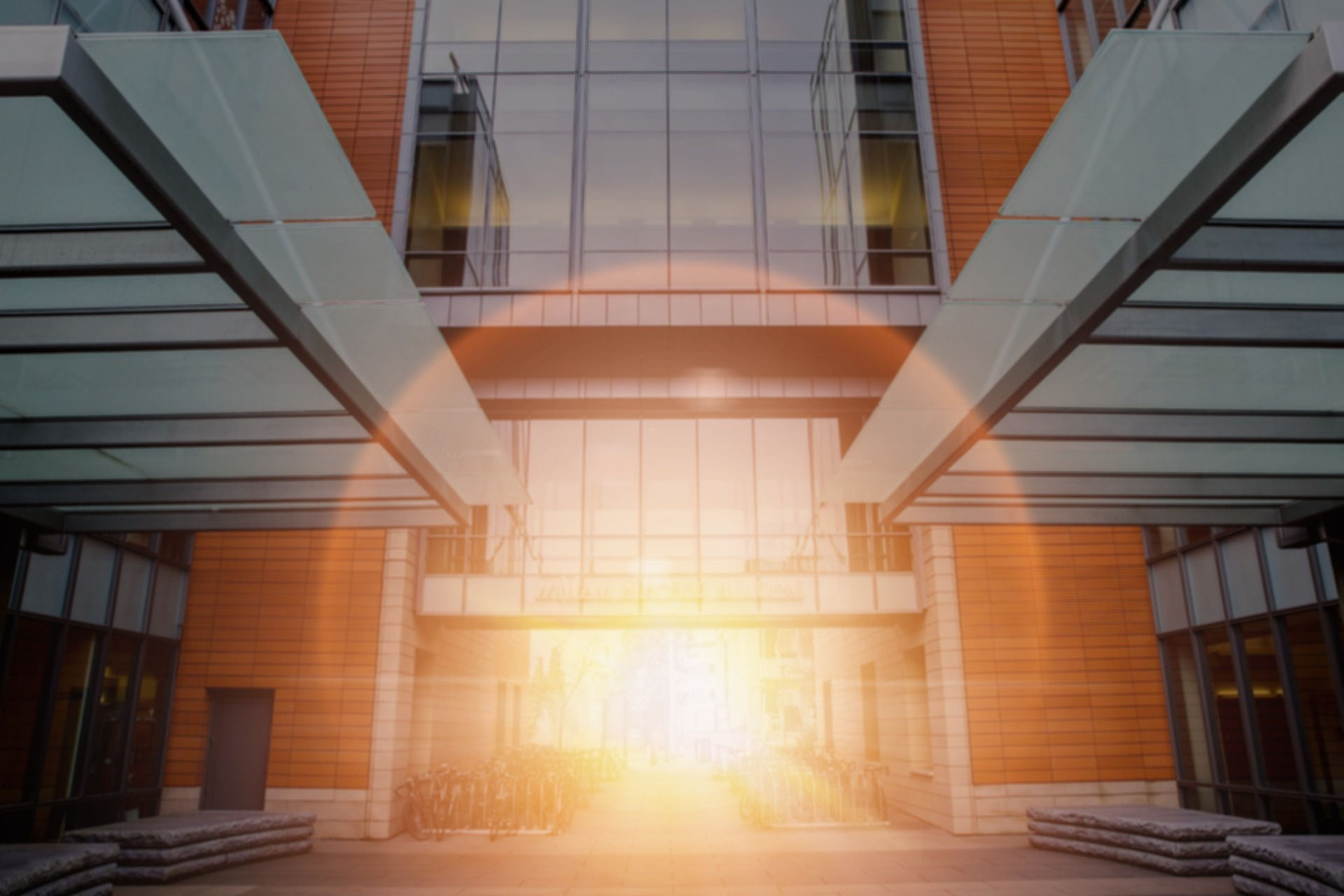
LIMB-SOCKET MOTION
The position of the residual limb in the socket and its change in position over time may provide meaningful information about how a person uses their prosthesis and how well it fits. Unlike interface stress sensing, an effort in which we have a long history (Interface Pressure and Shear Stress Analysis), limb motion sensing detects meaningful information while the foot is off the ground (swing phase) and during low weight-bearing activities. Limb vertical motion (pistoning) and body posture during sitting, for example, are well-characterized using limb motion sensing but not pressure sensing. Our efforts in this project have focused on developing a highly sensitive means for measurement and implementation in transtibial prosthesis users. Our goal is to use limb motion sensing system in prosthetics for training, diagnosis, and prognosis purposes
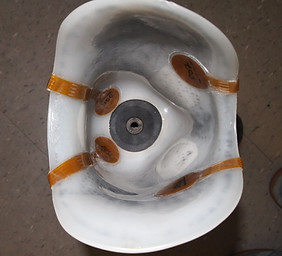

Project History
​
Initially, in our instrumentation development efforts we pursued means to detect walking speed (2000), distal limb position (2006), sock use (2012, 2013.2), and user activity (2013.1). These efforts resulted in functional technologies but we lacked a cohesive plan for how to implement them in clinical care. In 2014, Professor Brian Hafner (Rehabilitation Medicine, University of Washington) with us published a paper presenting a strategy for how prosthesis sensors might fit into three important aspects of rehabilitation - training, diagnosis, and prognosis (2014). We focused on creating a sensing system that has the potential to provide important clinical insight during all three phases.
​
In a subsequent study, we effectively used proximity sensors within the socket and accelerometers on the limb to detect user activity (2016.2). This system effectively distinguished doffed, walking (including all types of movement), standing, and sitting. However, the thigh accelerometer, which was attached to the liner over the anterior thigh, was bothersome to some participants. Interested in extending to a more detailed characterization of the limb-socket interface, we placed various sensors within 3D printed inserts that we custom-designed for each participant (2016.1, 2017, 2018.2). This system allowed flexibility in sensor selection and placement. Using different sensing modalities simplified interpretation of field collected data. An inductive sensor that we placed in the distal region of the socket provided promising insight towards monitoring sock use. We believe that the printed insert technology has a place in early fitting assessment since during this time the practitioner changes the socket shape frequently, and the capability to frequently manufacture new instrumented inserts would be a benefit. Our focus shifted to improvement of the promising inductance sensing modality, and we created a novel inductive sensing system for further investigation. Using the sensor on participants with a definitive prosthesis, we taped the sensor antennae to the inside of the socket. A conductive fabric target was adhered to the outside of the liner. We implemented this system to monitor user activity in multi-week take-home testing (2018.1). In a study on 21 participants, we characterized prosthesis day duration, how often people changed their sock thickness, and how long they temporarily doffed their socket during the day. While the sensor was effective, the target, the conductive fabric, was prone to degradation which electron microscopy revealed was due to microcracks within the conductive fibers. The cracks formed as a result of the mechanical stress from the residual limb. Using a modified version of the sensor that eliminated this problem during two weeks of take-home use, Professor Geoff Balkman (Rehabilitation Medicine, University of Washington) in a study on three participants found substantial differences between prosthetists' estimates of their patients' prosthesis use and data measured by the monitor, alluding to the well-established challenges in obtaining accurate information related to patient activity (2019.1). We concluded that a better understanding of patients' true prosthesis use and activity can facilitate an evidence-based approach to clinical practice and mitigate prosthetists' reliance on patient-reported history.
From 2018 to 2020, we reported on several iterations of a new target design, a liner-embedded target, that served as a more seamless and durable sensing element (2018.3, 2018.4, 2019.2, 2020). The target material is a small amount of iron powder that is embedded beneath the surface; it does not contact the user. This design differed from our previous effort in that the target was a magnetically permeable material instead of a conductive material. This change eliminated the microcrack problem and its associated durability issue described above. When used with a socket that had the antennae taped to the surface (see socket figure above), the new liner proved considerably more durable and a reliable signal was obtained. In a study on four participants, we demonstrated solid detection accuracy for identification of sit, seated shift, stand, standing weight-shift, walk, partial diff, and non-use (full doff) (2022.1). It was clear that step count may provide an incomplete picture of prothesis use, and larger studies should be pursued to investigate how bodily position and type of activity may facilitate clinical decision-making. In a subsequent study collecting data from 14 participants in their at-home environment, we were able to distinguish walking bouts from low commotion activity, helping to distinguish participants who used their prosthesis to move around in a confined space from participants who walked long distances (2022.3). This distinction may help practitioners to better identify their patients' componentry needs.
​
We approached prosthetic liner manufacturers to see if they could manufacture the ferrous liners, i.e., place a trace amount of iron powder in their product, for our research projects. One company was able to do so, and this advance has helped simplify our clinical study execution. We continue to make ferrous liners in our lab for participants who cannot wear the company's type of liner. Also, we enhanced the sensor sockets by embedding the antennae within the socket during fabrication (2022.2), an advancement that has essentially eliminated sensor failure problems. Testing the new system in participants with transtibial amputation revealed that as a socket was slowly enlarged, the sensors picked up the early signs it fit deterioration well before an experience research prosthetist was able to visually detect a change, and well before the participant indicated a sock ply change was needed (2021.1). Our current efforts are directed towards use of the limb motion sensing system in clinical prosthetics for training, diagnosis, and prognosis purposes.
​
In parallel with creating a technology to monitor motion at the limb-socket interface, we developed a sensor to detect locking pin vertical motion (2021.2). Similar to the limb-socket interface technology, this sensor uses an inductive sensing modality. We recently improved the versatility of the pin motion sensor and used it in a study on three participants during week-long take-home use. Results are forthcoming (2022.4).
Publications
2022.4. "Does sensing locking pin position provide relevant information towards clinical care?" (in preparation)
2022.3. "Beyond step counts and cadence: Classifying prosthesis use using a portable limb-socket motion sensor." (in preparation)
2022.2. "Fabricating sockets with distance sensors for prosthesis use and socket fit monitoring: Technical note." (submitted)
2022.1. "A novel portable sensor to monitor bodily positions and activities in transtibial prosthesis users."
2021.2. "A sensor to monitor limb depth in transtibial sockets with locking pin suspension."
2021.1. "Performance of a sensor to monitor socket fit: Comparison with practitioner clinical assessment."
2020. "Incorporating a ferrous polymer target into elastomeric liners for prosthesis users: A means for socket fit sensing."
2019.2. "Thin magnetically permeable targets for inductive sensing: Application to limb prosthetics."
2019.1. "Prosthetists' perception of information obtained from a lower limb prosthetic monitoring system: A pilot study."
2018.4. "An inductive sensing system to measure in-socket residual limb displacements for people using lower-limb prostheses."
2018.3. "Development of a magnetic composite material for measurement of residual limb displacements in prosthetic sockets."
2018.2. "Instrumented socket inserts for sensing interaction at the limb-socket interface."
2018.1. "A novel method for assessment of prosthesis use and accommodation practices of people with transtibial amputation."
2017. "Computer manufactured inserts for prosthetic sockets: A new tool for long-term prosthesis sensing."
2016.2. "Monitoring prothesis user activity and doffing using an activity monitor and proximity sensors."
2016.1. "Technical note: Computer-manufactured inserts for prosthetic sockets."
2014. "Considerations for the development of sensing and monitoring tools to facilitate treatment and care of persons with lower limb loss."
2013.2. "A novel measurement device for volume management in lower limb amputees: A technical note."
2013.1. "Classifying prosthetic use via accelerometry in persons with trans-tibial amputation."
2012. "Device to monitor sock use on people using prosthetic limbs: Technical report."
2006. "A noncontact sensor for measurement of distal residual-limb position during walking."
2000. "An accurate inexpensive system for the assessment of walking speed."