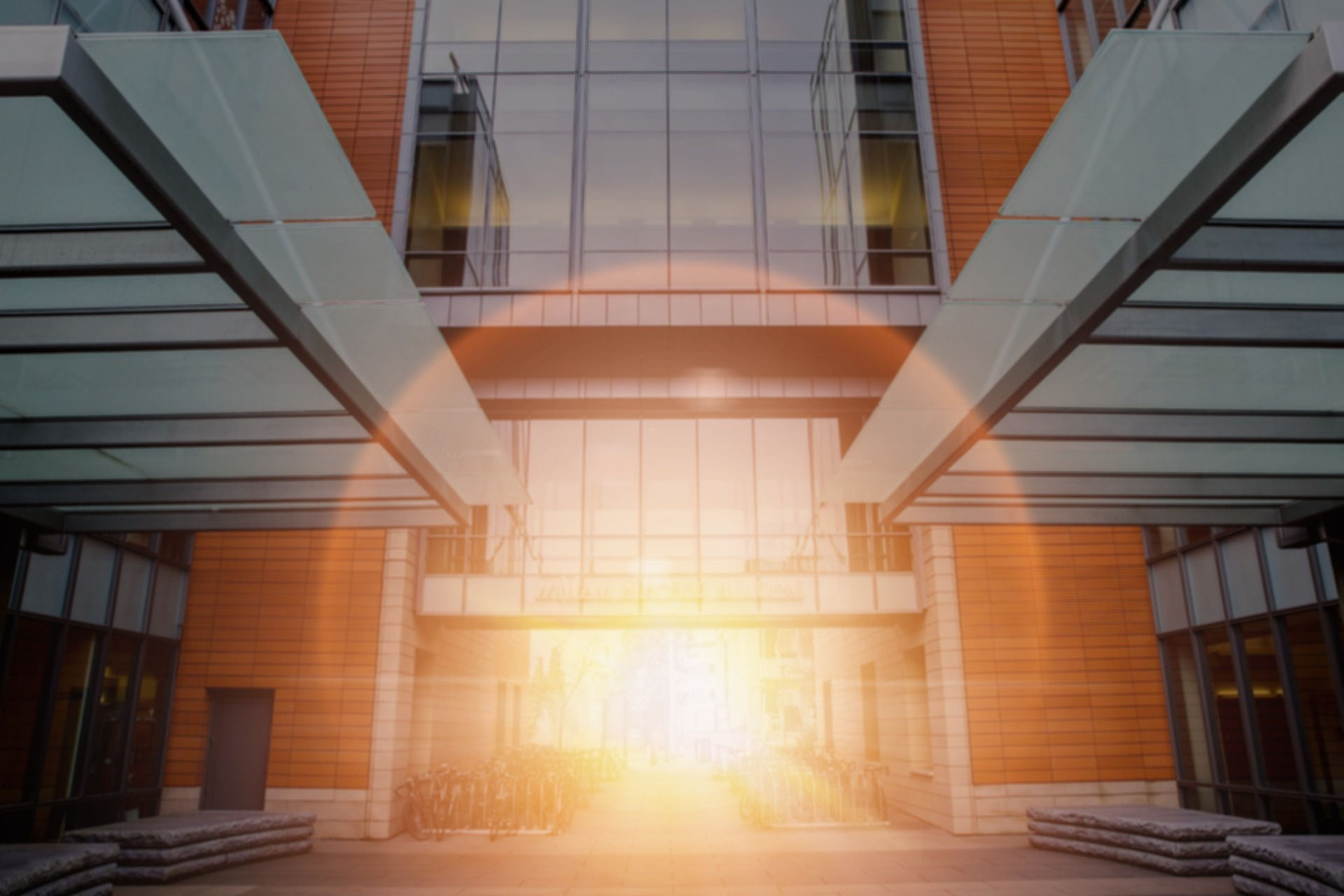
People with limb amputation struggle with the comfort, fit and function of their prosthesis on a daily basis. Licensed certified prosthetist Kate Allyn from the University of Washington (UW) explains: “Very small changes in the size of a person’s residual limb change how the prosthesis feels. Over the day, the socket may become uncomfortable and cause pain, instability, compensatory strategies or injury to the user.”
UW clinicians and bioengineers have solved this problem by creating a socket that automatically changes size as the user’s limb changes size. Participants say that the new socket solves their biggest challenge: “I don’t have to think about my socket, if I should stop and take my prosthesis off to add or remove socks. Everything is taken care of. I can focus on my life, what I am doing, playing with my kids. This is an amazing technology.”
The UW group developed the technology as part of a $6 million Joint Warfighter grant from the U.S. Department of Defense. Only 30 of these grants are awarded every three years in all areas of medicine. Bioengineering Professor Joan Sanders explains, “The grant allowed us to hire a lot of people to focus on a very innovative idea. The idea emerged in part from an article in a NASA magazine noticed by one of our Bioengineering PhD students, Christian Redd. The article described a new sensing chip and antenna that he realized perhaps could be used to monitor socket fit. Combining the sensing idea with the lab's experience in prosthetic engineering, Allyn’s and Drs. Janna Friedly's and Brian Hafner's (Rehabilitation Medicine Professors) clinical insight, another group member’s expertise in Chemistry (Ethan Weathersby), the group’s mechanical design team’s skills (Jake McLean, Brian Larsen, Andrew Vamos, Matthew Weissinger) and Mechanical Engineering Professor Joe Garbini’s expertise in control systems, the team was able to quickly create a socket that sensed limb-socket distance and continually adjusted socket size to maintain a consistent distance and consistent socket fit.
“This project was a home run from the start,” explains Sanders. Our first prototype worked well, and the innovations kept on coming to make it better, smarter and faster. Much of the credit goes to the prosthesis user participants who spent countless hours testing our technology and providing feedback. “They are the stars of this effort.”
The UW group has started a new grant to test the technology at the Center for the Intrepid (CFI) in San Antonio, Texas, a rehabilitation facility that provides rehabilitation for Operation Iraqi Freedom/Operation Enduring Freedom casualties who have sustained amputation or limb disability. Working with CFI principal investigator Lee Childers PhD and his team, the group is testing the auto-adjusting socket in a simulated ambush setting called the Computer Assisted Rehabilitation Environment (CAREN) and in a military functional evaluation test called the Functional Capacity Evaluation – Military (FCE-M). The UW team is honored to work with this community and help injured service members return to a level comparable to or higher than before their injury.